Milhões de baterias de íon-lítio saem, todos os dias, das fábricas desses componentes fundamentais para notebooks, celulares e, sobretudo, veículos elétricos. O descarte dessas células de energia, porém, ainda desafia a indústria e os pesquisadores da área, especialmente porque a indústria automobilística já está colocando em prática projetos para acelerar a transição elétrica. Depois de 10 anos de uso, parte dessas baterias veiculares podem ser usadas como bancos de energia em usinas eólicas ou fotovoltaicas. Mas, após algum tempo, elas se convertem em lixo. Ou melhor, em resíduos metálicos com potencial para reaproveitamento.
Para atender a esse mercado potencial, algumas empresas começam a se estruturar em várias partes do mundo. A Redwood Materials, por exemplo, é uma pequena empresa fundada em 2017 exatamente para converter velhas baterias em matérias-primas para novas células.
Na última década, a produção de íons de lítio aumentou dez vezes para atender à crescente demanda por veículo elétricos (EVs). Agora, os veículos daquela primeira onda de produção estão apenas começando a chegar ao fim de sua vida útil. Isso marca o início de um "tsunami" de baterias gastas, que só vai piorar à medida que mais carros, ônibus, caminhões, e até bicicletas elétricas entrem em circulação. A Agência Internacional de Energia prevê um aumento de 800% no número de EVs na próxima década, cada carro com milhares de células. A reciclagem de íons de lítio parece ser a única saída.
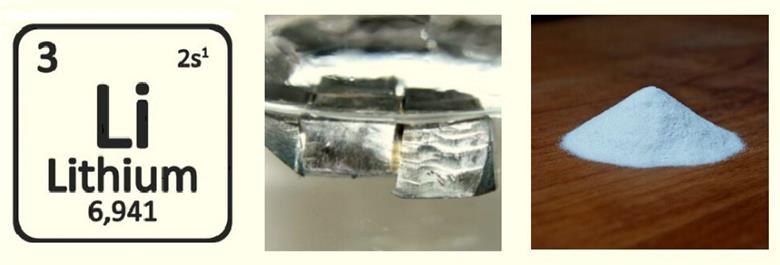
Litio reciclado pela Redwood pelo processo de pirometalurgia e hidrometalurgia Foto: Redwood
O fundador da Redwood, J. B. Straubel, entende o problema melhor do que a maioria. Afinal, ele desempenhou um papel significativo em sua criação. Straubel é cofundador e, até o ano passado, era diretor da Tesla, uma das maiores fabricantes de carros elétricos. Durante seu tempo lá, a empresa cresceu de uma startup vendedora de carros esportivos para a fabricante de automóveis mais valiosa do planeta. Ao longo do caminho, a Tesla também se tornou uma das maiores produtoras de baterias do mundo. Straubel vê essas baterias não como um problema, mas como uma oportunidade.
Existem duas maneiras principais de desfazer as baterias de lítio. A técnica mais comum, chamada pirometalurgia, envolve sua queima para remover materiais orgânicos e plásticos indesejáveis. Esse método deixa a recicladora com apenas uma fração do material original - normalmente apenas o cobre dos coletores de corrente e níquel ou cobalto do cátodo. Um método de pirotecnia comum, chamado de fundição, usa um forno de combustíveis fósseis, o que não é bom para o meio ambiente e provoca perdas de alumínio e lítio no processo. Mas é simples, e as fundições que existem atualmente para processar o minério da indústria de mineração já estão aptas a movimentar baterias. Da pequena fração das baterias de lítio que são recicladas nos EUA - cerca de 5% de todas as células gastas - a maioria acaba em um forno de fundição.
A outra técnica é chamada de hidrometalurgia. Uma forma comum dessa técnica, chamada lixiviação, envolve a imersão das células de íon-lítio em ácidos fortes para dissolver os metais em uma solução. Mais materiais, incluindo lítio, podem ser recuperados dessa forma. Mas a lixiviação traz seus próprios desafios. Os recicladores devem pré-processar as células para remover invólucros plásticos indesejados e drenar a carga da bateria, o que aumenta o custo e a complexidade. Isso explica, em parte, porque as baterias velhas de lítio têm sido tratadas como lixo desde que as primeiras células comerciais chegaram ao mercado no início dos anos 1990. Muitas vezes era várias vezes mais barato minerar novo material, especialmente lítio, do que recuperá-lo com o processo de lixiviação.
A empresa Redwood usa uma combinação de pirometalurgia e hidrometalurgia para recuperar os materiais. Os operários vestem roupas de calor reflexivas e trabalham para "cozinhar" as baterias em conversores, de forma a separar os metais. Em vez de usar combustíveis fósseis para queimar o material, como em um processo de fundição convencional, a pirotécnica de Redwood usa a energia residual das baterias, como os orgânicos no eletrólito, para conduzir o processo de conversão. O que sobra é uma liga de metal que é filtrada por um processo hidrometalúrgico para recuperar compostos individuais.
O diretor Straubel afirma que com essa técnica pode recuperar entre 95% e 98% do níquel, cobalto, cobre, alumínio e grafite de uma bateria e mais de 80% do lítio. No momento em que uma bateria passa pela instalação de reciclagem de Redwood, ela foi dividida em seus ingredientes básicos - carbonato de lítio, sulfato de cobalto e sulfato de níquel - que ficam prontos para a fabricação de uma novabateria. “Vamos construir um ecossistema de remanufatura para todas essas baterias”,afirma Straubel. “O material pode ser reutilizado quase infinitamente. Não há degradação inerente aos átomos de metal."
Alguns desafios para a reciclagem do lítio decorrem do fato de que as instalações que os processam não foram projetadas especificamente para essa finalidade. mas as pessoas que já atuam nessa atividade esperam que a criação de instalações dedicadas melhore a economia do setor. “Estamos focados em um processo customizado, que é projetado especificamente para baterias de íon de lítio porque estamos começando a ver volumes maiores”, diz Tim Johnston, da Li-Cycle, uma recicladora canadense de baterias. “Historicamente, as baterias eram vistas como lixo, e buscamos virar isso de cabeça para baixo, focando nelas como um recurso.”
Pegada ambiental
A Li-Cycle se autodenomina a maior recicladora de íons de lítio da América do Norte e tem uma abordagem de recuperação diferente da Redwood. O processo da empresa pula totalmente a fundição e refina a bateria apenas com a lixiviação. Primeiro, eles jogam as baterias em um tanque que simultaneamente as descarrega e destrói. Em seguida, as células passam por etapas de banhos químicos para liberar os metais.
O processo converte quase tudo de volta em matéria-prima utilizável - o plástico do separador da bateria é transformado em flocos, os coletores de corrente são transformados em folhas de cobre e alumínio, o grafite do ânodo é transformado em um concentrado de carbono e os materiais do cátodo como níquel, cobalto e lítio são recuperados individualmente para novas baterias. “Não produzimos nenhuma quantidade significativa de resíduos”, afirma Johnston. “Não produzimos nenhuma quantidade significativa de emissões atmosféricas, não produzimos água residual e tudo é feito em baixa temperatura. Nossa pegada ambiental é muito pequena”, afirma o empresário.
Sem dúvida, a inovação mais significativa na Li-Cycle não são os processos químicos, mas o design das próprias instalações de reciclagem. A Li-Cycle processa as baterias em diferentes locais nos EUA e Canadá, em fábricas modulares que transformam as células de lítio em uma massa negra, que depois é processada para liberar os metais.
Reciclagem direta
Em 2019, o Departamento de Energia do governo dos EUA contratou o Laboratório Nacional de Argonne para liderar seu centro ReCell, que se concentra no aprimoramento das técnicas de reciclagem de íons de lítio. Os cientistas do centro encontraram alguns processos de reciclagem direta, que evita o desmonte da estrutura cristalina das células. “O objetivo do centro é chegar a algo que convença a indústria a assumir isso”, disse Linda Gaines, cientista-chefe do ReCell Center e analista de sistemas de transporte do Argonne National Laboratory. “Precisamos responder a todas as perguntas sobre como isso vai ficar quando for ampliado.”
O desafio da reciclagem direta é que as células não são projetadas para serem recicladas. São fabricadas para produzir energia por um longo tempo e da forma mais barata possível. De um modo geral, a reciclagem não é nem mesmo uma consideração tardia. E isso torna difícil o processo de desempacotar. Células individuais são sistemas complexos que têm vários componentes quimicamente distintos misturados - às vezes soldados - em um pequeno volume. Torna-se um desafio extrair sem a ajuda de ácidos fortes ou temperaturas extremas.
Por enquanto, Gaines e seus colegas estão focados em descobrir como salvar a estrutura das baterias que já existem. No futuro, no entanto, é possível que as baterias sejam feitas para serem recicladas, mas apenas se isso for econômico e não afetar o desempenho. “Projetar para a reciclagem é uma área muito importante, mas você não pode sacrificar o desempenho de forma alguma, ou ninguém vai querer fazer isso”, diz Gaines.
Ainda assim, há muitas outras mudanças que podem ser feitas na maneira como os sistemas de bateria são fabricados para melhorar os esforços de reciclagem, diz Carlton Cummins, da Aceleron. Ele foi cofundador da empresa em 2015, depois de começar a pesquisar o que fazer com os veículos elétricos quando eles envelhecem e “perceber que pode-se reutilizar a maior parte do carro, exceto a bateria”, diz ele.
“As baterias não foram projetadas para reparo, reutilização ou atualização. O foco principal na época era construí-las de forma econômica e rápida”. Como resultado, as células usadas em EV e baterias de armazenamento estacionário tendem a ter várias soldas por bateria que conectam dezenas de baterias para que possam ser controladas como uma unidade. Cummins diz que esta é uma técnica de conveniência emprestada da indústria de eletrônicos de consumo, mas torna as baterias automotivas mais difíceis de desmontar para atualizações ou reciclagem.
A solução da Aceleron para o problema é aparentemente simples. Cummins e sua equipe projetaram uma carcaça que pode ser usada para uma variedade de tipos de células diferentes, sem conexões soldadas. A plataforma de bateria comprime as células em um case rígido e usa um circuito removível para conectá-las. Isso significa que se uma célula individual falhar, ou se o proprietário do pacote quiser atualizá-la para uma bateria melhor, as células podem ser trocadas afrouxando algumas porcas e parafusos. “Da maneira como as baterias são projetadas hoje, tudo é soldado e colado, e a suposição é que no final do uso seja descartado”, diz Cummins. “Tivemos que reinventar a forma como você monta baterias com algo que é projetado para reutilização, bem como reciclagem.”
Ainda há uma série de desafios técnicos, políticos e econômicos que os recicladores de íon de lítio terão que enfrentar, e o sucesso não é garantido. O cobalto, por exemplo, é o material mais caro na maioria das baterias de veículos, mas os fabricantes de baterias estão buscando novas soluções, sem cobalto. A nova geração de recicladores de bateria está apostando que poderá encontrar uma maneira de fechar o ciclo na cadeia de suprimentos de íons de lítio e ganhar dinheiro com isso. Esperamos que eles estejam certos.
*Artigo publicado originalmente no site da revista Wired em 30/11/2020. Tradução e adaptação de Marcos de Sousa/Mobilize Brasil
Leia também:
Programa vai acelerar transição para ônibus elétricos na América Latina
Ônibus elétrico movido a energia solar começa a circular no Ceará
Carros híbridos são "desastre ambiental", denuncia estudo europeu
Nova linha de BRT operado por trólebus inicia testes na Itália
Prefeito eleito promete 'fazer de Belém a capital nacional das bicicletas'